Lenkung
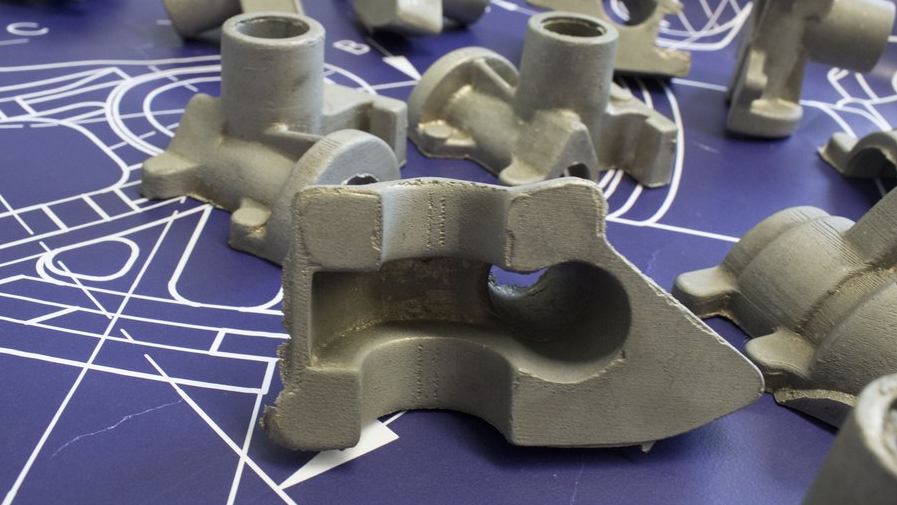
Neben Gussheck und Invertergehäuse sind die Gehäuse für die Lenkung wohl mit die komplexesten Gussteile am Auto. In dieser Saison entwarfen wir drei Gehäuse, eines für unser Kegelradgetriebe und zwei für unsere Zahnstangen, je eins für Vorder- und Hinterradlenkung. Jedes Gehäuse besteht aus einer linken und einer rechten Hälfte. Dies ermöglicht einen einfach Zusammenbau. Außerdem werden für den Guss keine Kerne benötigt, da es keine Hinterschnitte gibt.
Für die Konstruktion gab es mehrere Zielstellungen: Es sollten alle Wellen und Lager fixiert werden, die Gehäuse mussten am Auto befestigt werden und natürlich müssten sie auch mit dem Sandgussverfahren gießbar sein, weshalb Hinterschnitte vermieden wurden sowie an entsprechenden Stellen Formschrägen einkonstruiert wurden.
Nachdem im CAD alles fertig konstruiert wurde und mit der Gießerei mögliche Probleme besprochen wurden, gingen die Daten nach Freital zu unserem 3D-Druck-Partner, der sowohl die Modelle der Gehäusehälften als auch Aufstampfhilfen für das spätere Einformen druckte. Die Modelle wurden dann von uns geschliffen um eine glatte Oberfläche zu erhalten. Zusätzlich folgte eine Behandlung mit THF-Dampf für eine noch glattere Oberfläche.
In der Gießerei wurde mit den Modellen eine Negativform aus Sand gebaut, in welche flüssiges Aluminum gegossen wurde. Die Gehäuse wurden anschließend wärmebehandelt um höhere Festigkeiten zu erzielen.
In der Zwischenzeit bereiteten wir die Fräsnachbearbeitung vor. Dazu ließen wir in eine Stahlplatte Gewindebohrungen fräsen sowie „Säulen“ drehen, die dann in die Platte geschraubt wurden. Diese benötigten wir zum Fixieren der Gehäuse beim Bearbeiten der Lagersitze. Eine andere Befestigung war nicht möglich.
Nach der Fräsnachbearbeitung folgte der Zusammenbau mit Lagern, Zahnrädern und Wellen sowie das Einstellen der Abstände, so dass die Lenkung möglichst spielfrei wird.
Wir danken SEs Solutions für den Druck aller benötigten Kunstoffteile für den Guss, der Georg Hermann Metallgießerei für den Guss selbst, Konnerth & Co für die Fräsnachbearbeitung, sowie der Werkstatt der Fakultät 4 für das Fräsen der Stahlplatte, Herrn Wolf vom Institut für Metallformung für das Drehen der Stahlteile und Herrn Lißner vom Institut für Physikalische Chemie für die Unterstüzung beim THF-Bedampfen.