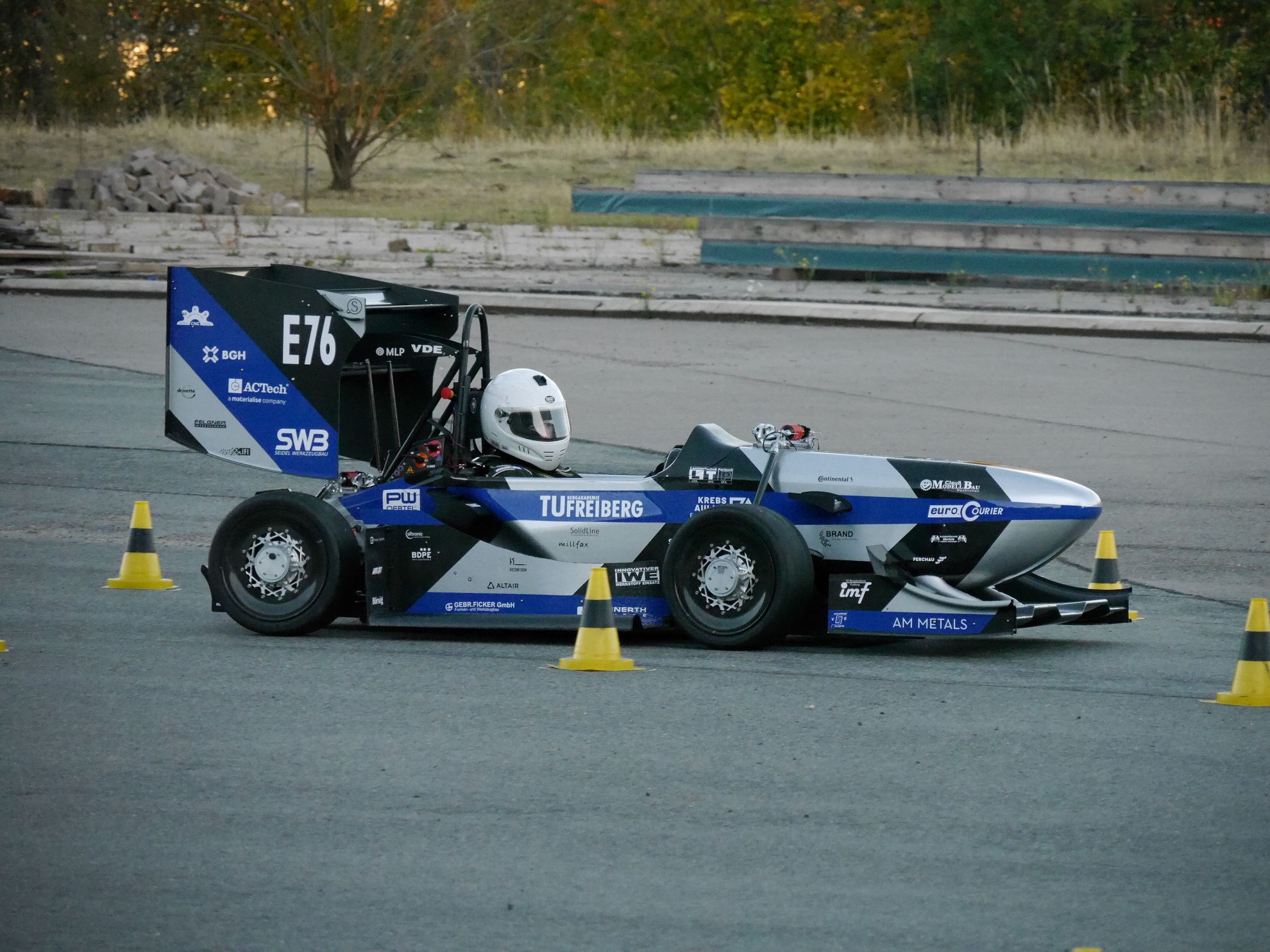
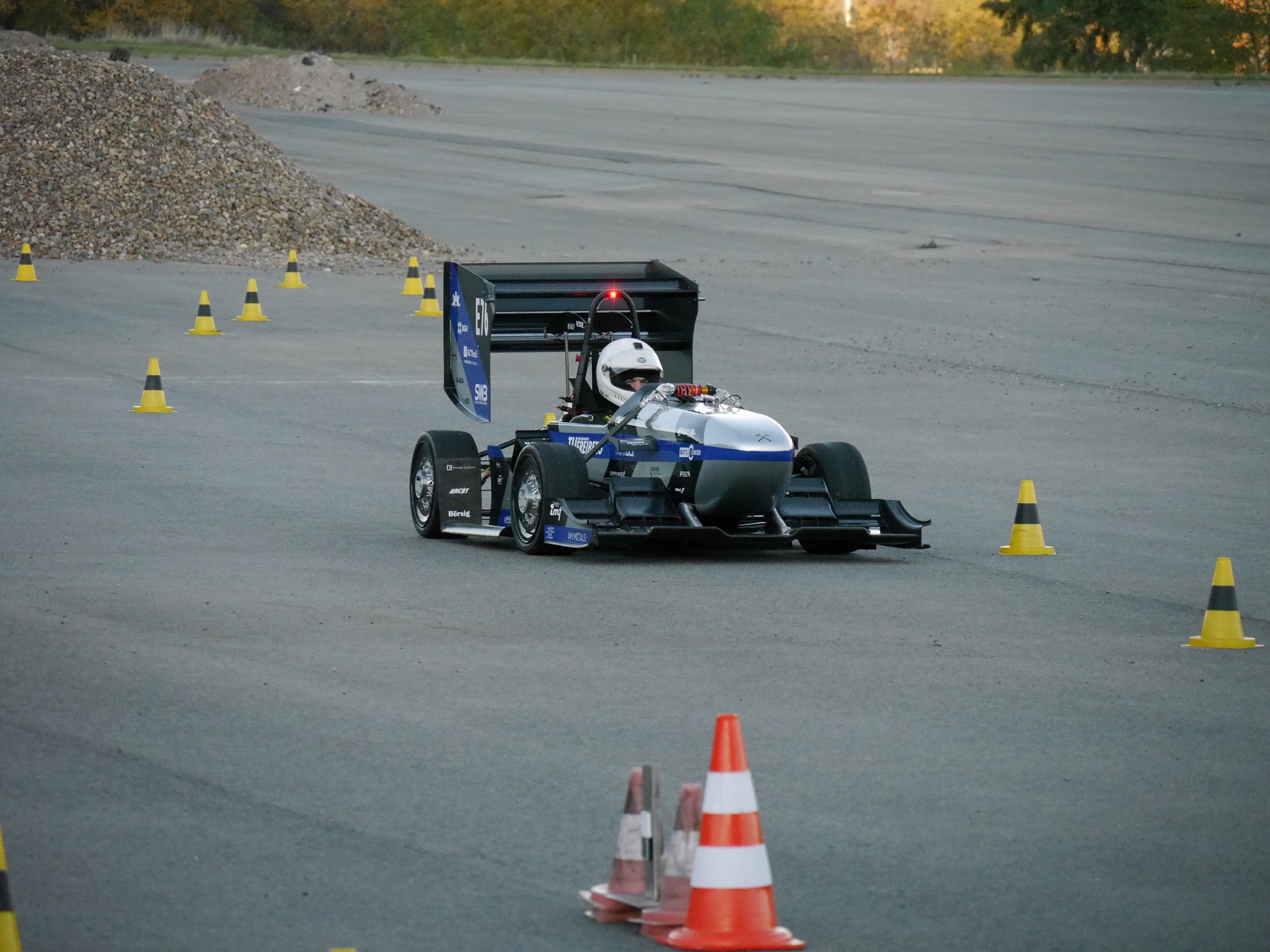
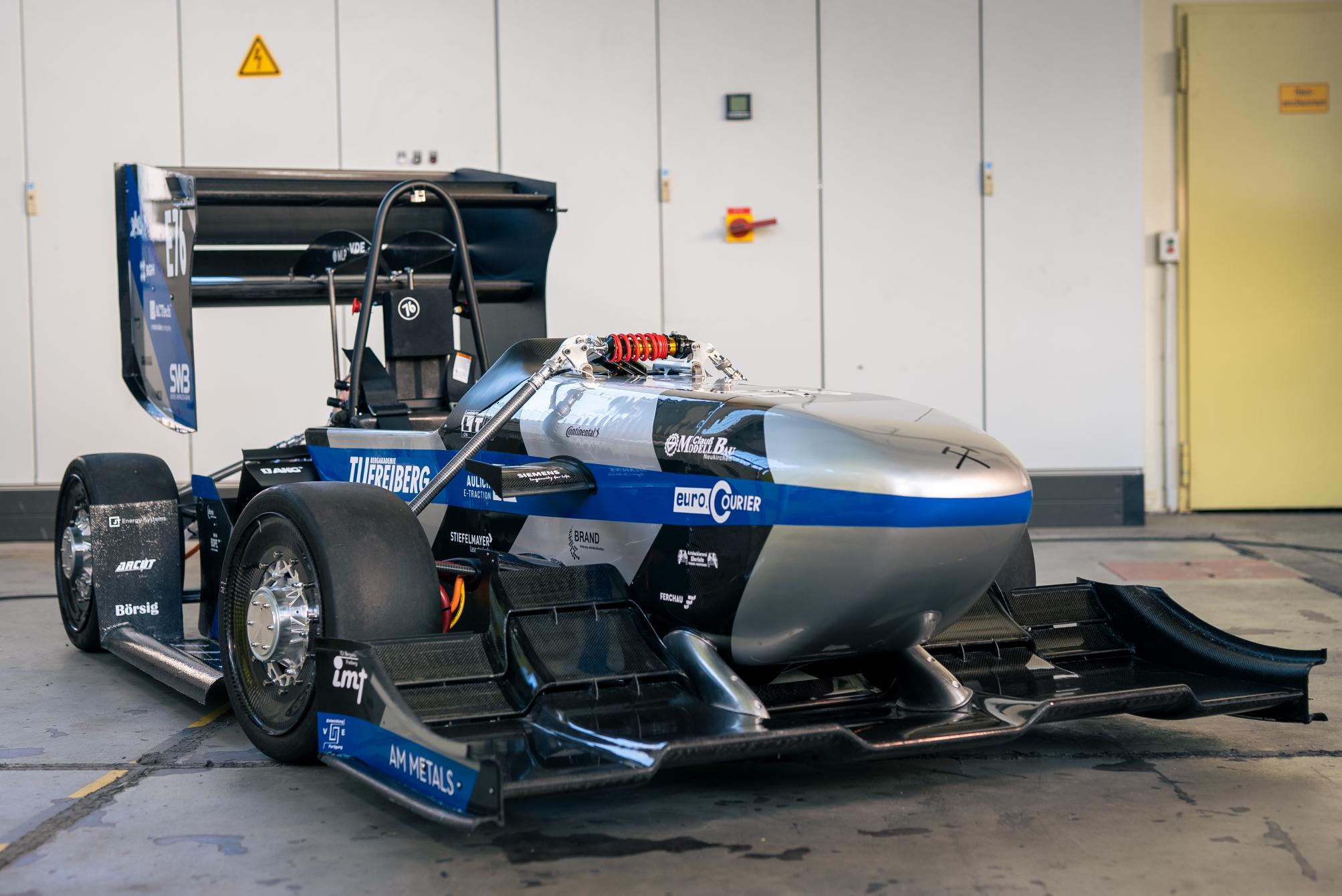
DSC09257
DSC09257
MicrosoftTeams-image (4)
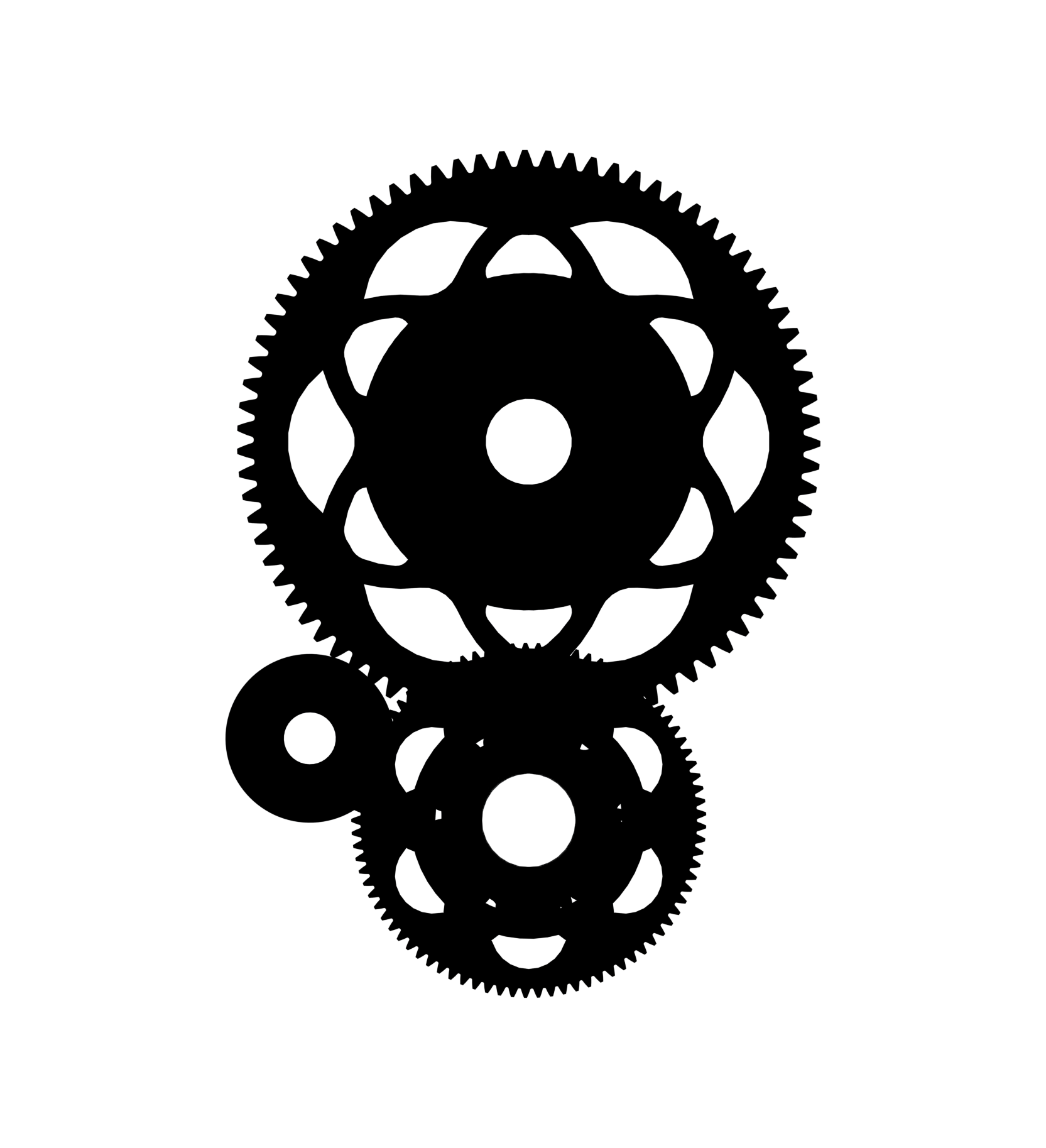
Mechanical Drivetrain
- Motor: self-developed wheel hub motor, all-wheel drive
- Power: 37 kW per motor
- Torque: 31 Nm per motor
- Transmission: self-developed 1.5-stage planetary gear; transmission of 14
- Cooling: two separate cooling circuits for motors and inverters
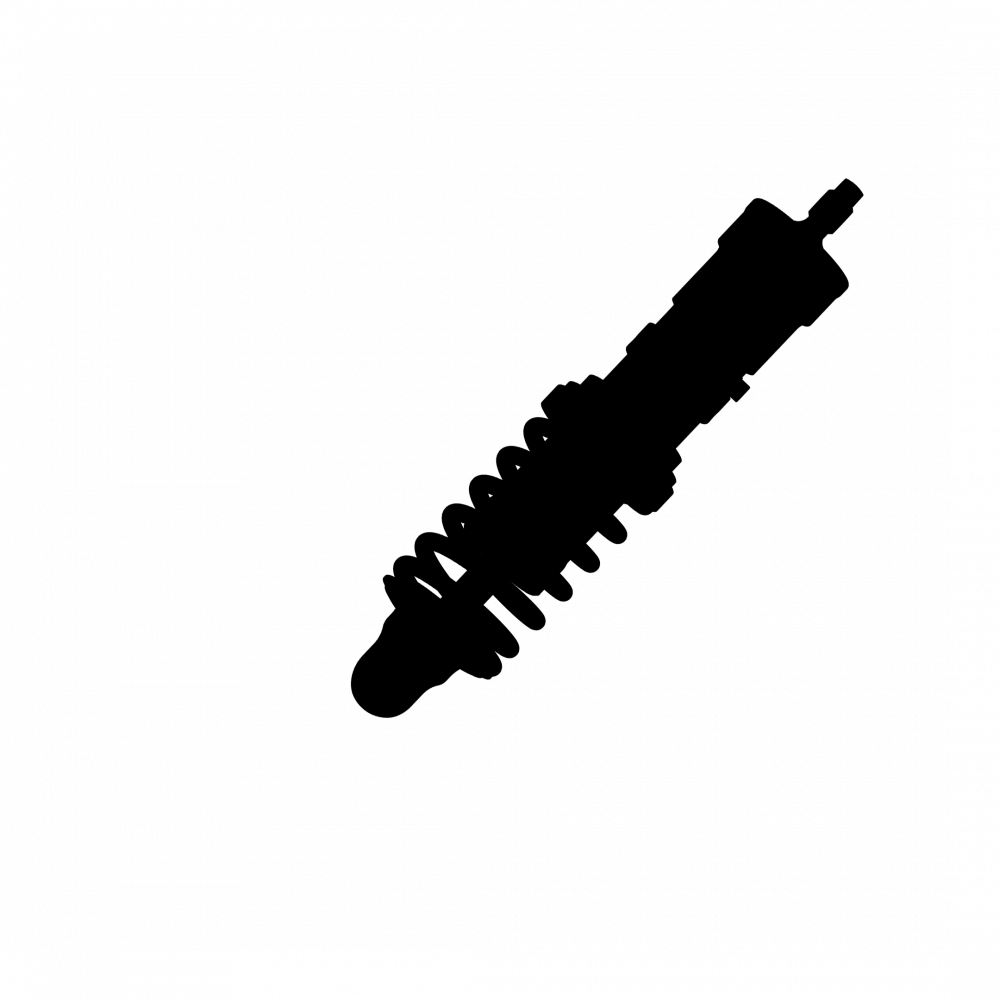
Suspension
- Wheel suspension: CFRP double wishbone axles
- Upright: Topology-optimized DMLS structure made of high-strength aluminum (front axle)/ investment cast structure made of AlSi7Mg0.6 (rear axle), integrated transmission mount and motor cooling
- Spring damper system: Heave-roll decoupled system with air spring on the roll damper, actuated via pushrods
- Wheel hub: milled aluminum structure from EN AW 7075 T6
- Brake system: self-developed brake calipers for front and rear axle made of high-strength aluminum
- Rims: 13" CFRP-rim with aluminium rim star
- Tires: 13" Continental Slick C20
- Wheelbase: 1530mm
- Front and rear track width: 1220mm
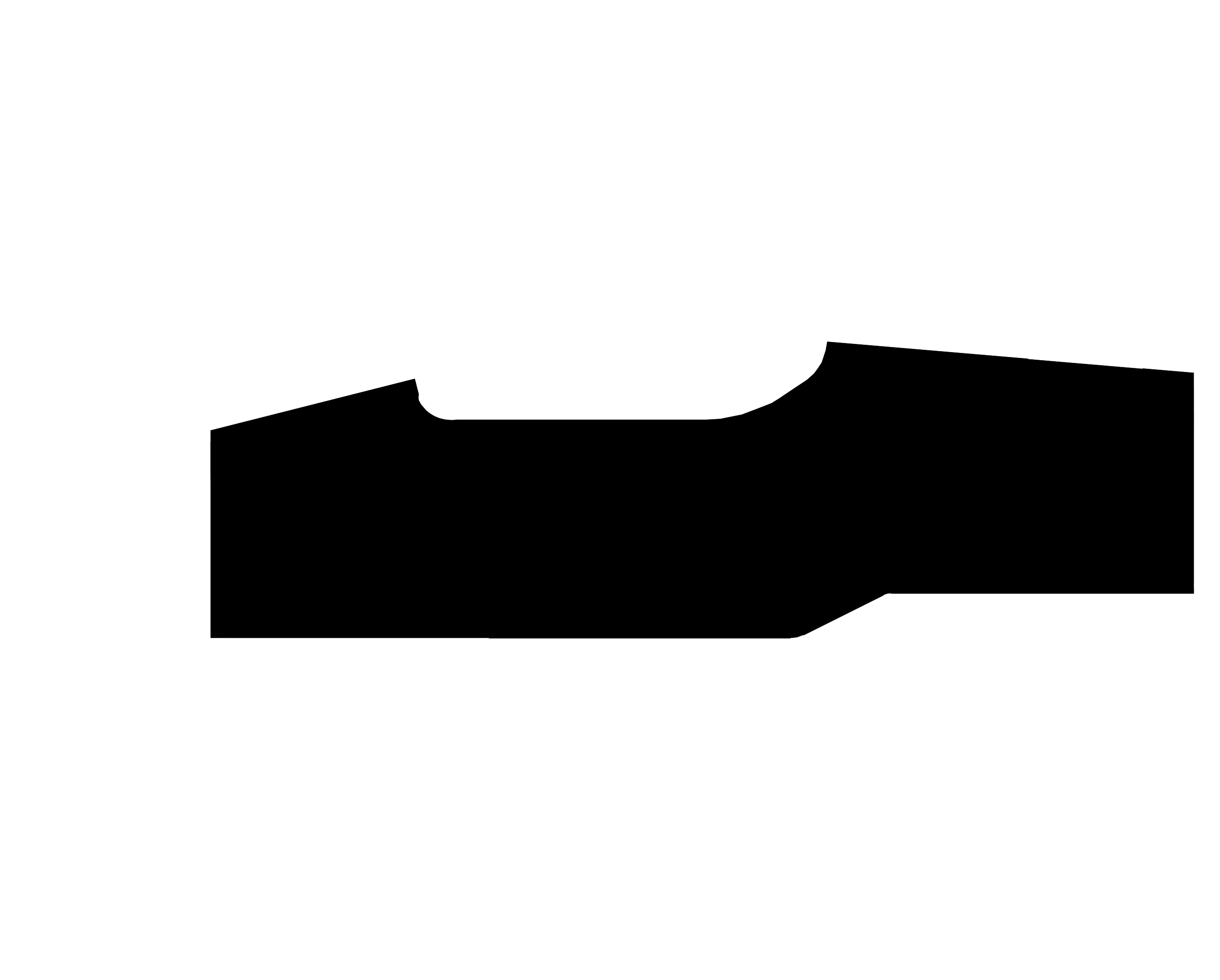
Chassis
- Monocoque structure: Hybrid monocoque with CFRP (middle) or aluminum cover layers (front & rear) as well as aluminum honeycomb and hard foam as core material; magnesium inlays at attachment points
- Accumulator housing: consisting of CFRP sandwich with aluminum honeycomb core and serial cooling
- Pedals: Accelerator and brake pedal made of aluminium
- Safety structures: Main roll hoop made of steel, alumium front roll hoop laminated in monocoque; crashbox made of an aluminum honeycomb and aluminium plate
- Ergonomics: CFRP seat; CFRP steering wheel; 6-point harness; pedals adjustable to driver size
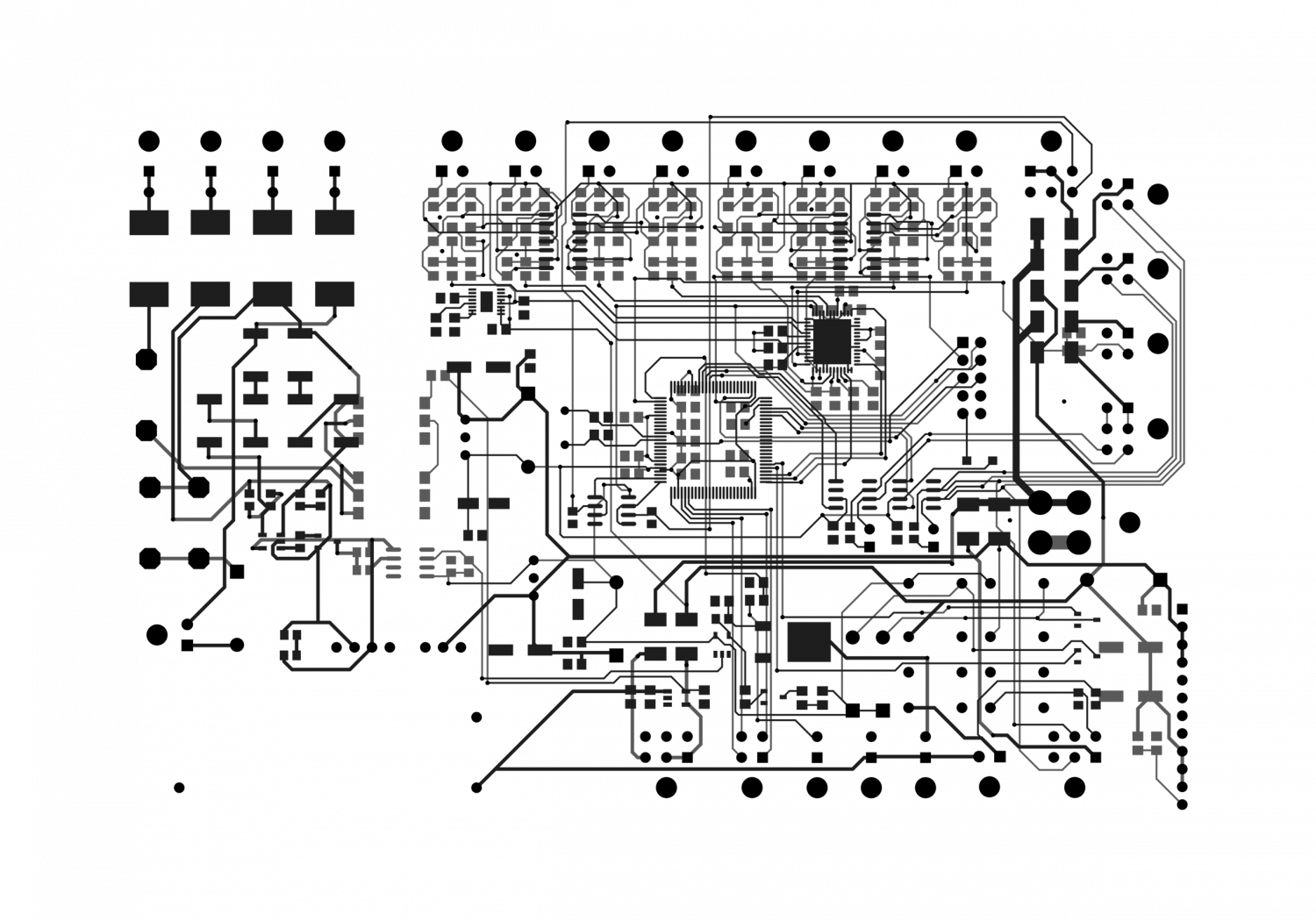
Electronics
- Accumulator: total capacity of 6.9 kWh, 596 V maximum voltage, 284 lithium-polymer cells in a 142s2p connection, self-developed Accumulator Management System (AMS)
- Power electronics: 2x Lenze-Schmidhauser double inverter 60 kW in the self-developed investment casting housing
- Low voltage system: Modular system of self-designed circuit boards for:
- Measured value acquisition
- Driver interface
- Vehicle supply
- Vehicle dynamics control
- Security systems
optional tire temperature sensors to optimize the chassis setup - Driving dynamics control: consisting of torque vectoring (with yaw rate control), assessment of the vehicle condition, traction control, range control and performance derating and failsafety; cycle time 2 ms
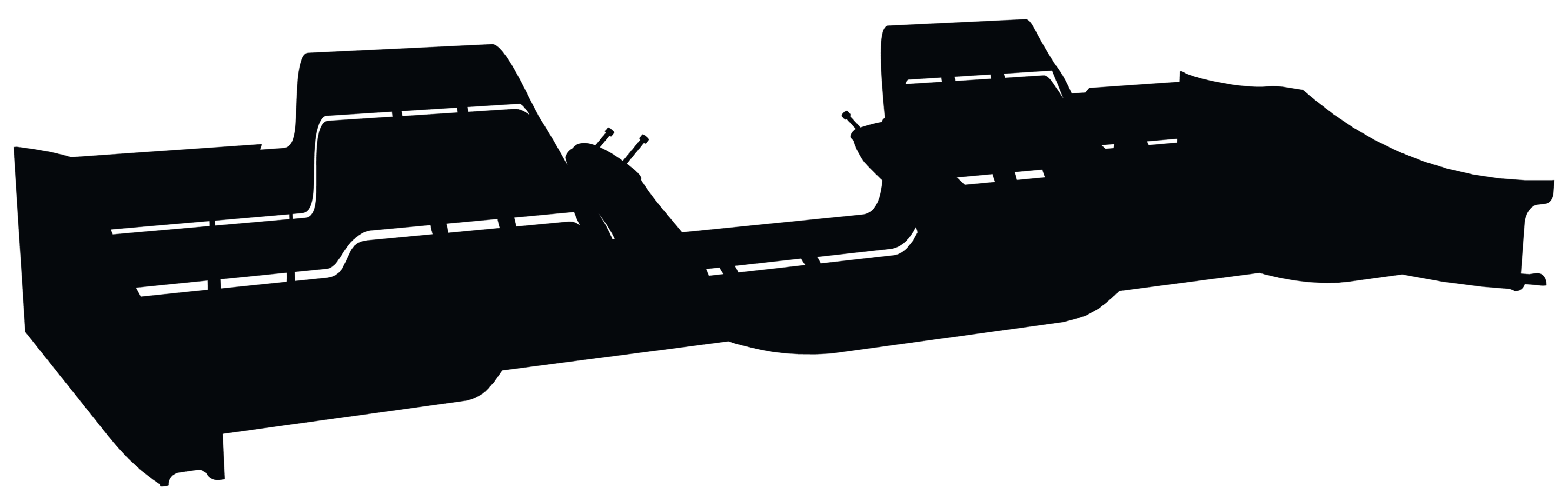
Aerodynamics
- CFD-optimized vehicle
- Validated with load cells / flow visualization
- Coefficient of Lift * A: -5.95 [m^2]
- Lift / Drag: -3.24
- Package weight: 16 kg
- Highlights:
- Optimization of the monocoque shape for maximum side wing area and underbody downforce
- Wheel covers, bargeboards and fully covered front gear to control wheel airflow and reduce steering angle sensitivity
- Front wing and connection optimized for cross flow